![]() $220 SAVE $130 = 37.0% Western Digital 16.0TB Western Digital Ultrastar DC HC550 3.5-in… in Storage: Hard Drives
|
![]() |
![]() |
![]() |
![]() |
RV Batteries: Planning for Voltage Losses from Cabling and Battery
Photographer and cyclist and Mac expert and software engineer Lloyd Chambers is available for consulting on general Sprinter considerations at his usual consulting rates via phone, or in person in the Palo Alto, CA area. Save yourself hours and mistakes by discussing issues up-front. More about Lloyd....
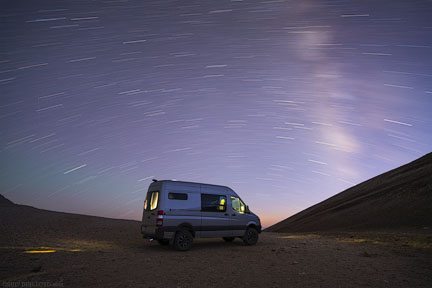
This discussion applies to both lithium and lead acid batteries, though the particulars with lead acid will be even worse as discharge continues due to dropping voltage. Dual battery setups are one way to supply more amperage with less voltage loss, but this is bulky and costly.
The challenge: as the amperage draw increases, the battery voltage decreases (for lithium or lead acid batteries).
Because the battery voltage itself can drop to the 12.6V range or below under heavy use (lower as discharge increases), the cabling from the battery to the inverter becomes critical. The total drop in voltage must be accounted for (battery voltage drop and drop due to cabling).
Reducing voltage losses
Three ways to reduce voltage losses.
- Dual or larger cables: the voltage drop from cabling could be cut in half using a huge 4/0 cable (not easy to wire through a panel), or dual 1/0 cables (equivalent to one 4/0 cable). This would cut the 0.5V loss @ 164 amps to 0.25V. But that would still only yield 12.37 volts—little headroom for more amperage, and dropping the DC-AC conversion efficiency as well. Both approaches have issues; 4/0 is hard to route/bend and dual 1/0 makes connectors awkward. See the voltage calculator.
- Use dual inverters: place some load on one inverter, and some load on another. This is a dual cable setup (one cable to each inverter).
- Use dual batteries in parallel: with each battery seeing only half the amperage draw and having its own cable, the battery voltage will drop less and in effect one uses dual cables. But for me, buying another $6K battery is not feasible, nor is there any space to include a 2nd battery. This is also in effect a dual cable setup.
- Reduce cabling length: cut voltage losses is by reducing cable length, which is why planning out wiring length (including fusing) is critical. Fusing in my case causes a longer cable run than otherwise necessary (battery to fuses, fuses to inverter). That situation is being rethought.
Dual 1/0 cables are equivalent to one 4/0 cable, so why not just use 4/0 cabling? Because aside from straight-line wiring, working with 4/0 is very difficult in terms of a wiring panel with fuses and solenoids or any place where the cable needs to bend. Thus the common suggestion of using 4/0 is simply not realistic in a small van like the Sprinter. Also, the connectors are a choke point and could get very hot with a 4/0 cable since the connectors to battery posts and inverter remain the same size with 4/0.
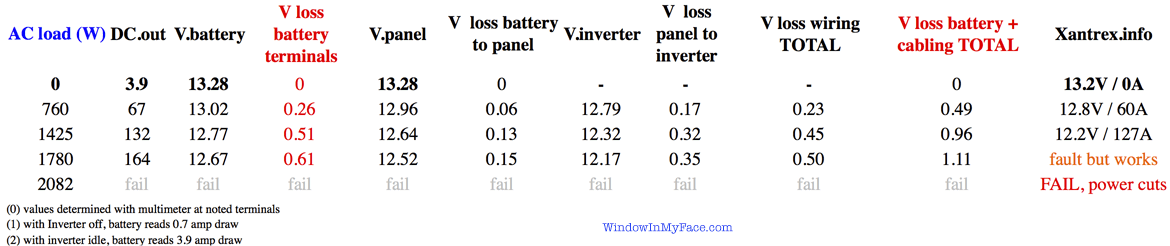
Lithionics 12V400A-5D-CTRL400 cabled to Xantrex 3012 with 10' 1/0 cable
Real world example
Upgrades/changes to original setup all told reduce voltage drop from resistance by 3X across every path. Testing at 132 amps DC @ 12.8V (1690 watts) and the Xantrex XC 2000W inverter, I found that with dual 1/0 cables, the connector ends do not even get warm under that load, so my setup with dual cables is a robust solution.
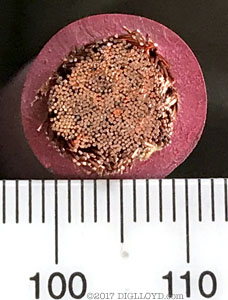
- Upgraded to use *dual* 1/0 cables from alternator to battery, and both cables 7 feet shorter than the original single cable. This decreases the resistance by about 3X.
- Upgraded to use *dual* 1/0 cables from battery to the wiring panel.
- Upgraded so that the wire from wiring panel to inverter is only about 18 inches of 1/0 cable; this is about 1/3 the length prior, cutting resistance by about 3X.
What follows below was the *original* (non upgraded) cabling.
This discussion uses measurements with the Lithionics 12V400A-5D-CTRL400 cabled to the Xantrex / Schneider Electric Freedom 815-3012 SW 3000 watt inverter/charger cabled together with a total of 10 to 12 feet of 1/0 size cable. As it turns out, that is/was insufficient for high amperage usage.
Real-world voltage losses are captured in the table below from data I obtained using a multimeter @AMAZON, measuring the voltage at 3 distinct points in the chain (at battery terminals, at cabling panel after ~4 feet of 1/0 cabling, at inverter terminals through 5 feet of 1/0 cable from panel).
As shown below, voltage at the terminals of the inverter drops to 12.17V at 164 amps using 1/0 size cables, which is 0.07V above the cutoff threshold of the Xantrex 3012 power inverter. Below that cutoff, it cuts off AC power, so more than about 170 amps means no AC power.
Note that 12.17V @ 164 amps is only 2000 watts, well below the rated continuous duty of 3000 watts for the Xantrex 3012. Clearly, battery and cabling are critical if one hopes to actually get 3000 watts out of an inverter.
See the voltage loss calculator. Real-world losses can be greater than calculated for various reasons.
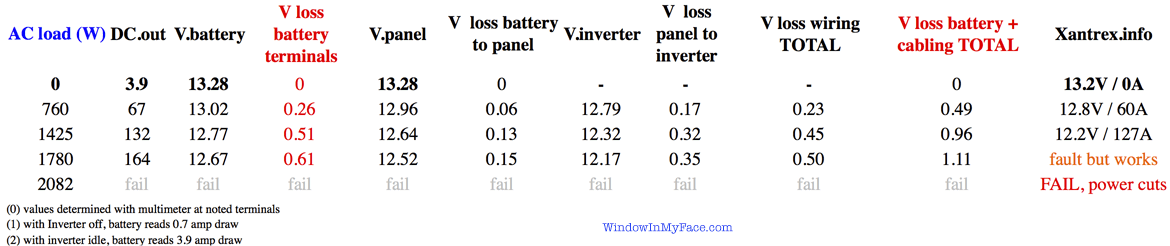
Lithionics 12V400A-5D-CTRL400 cabled to Xantrex 3012 with 10' 1/0 cable
Lithium batteries in sub-freezing temperatures
This was my #1 concern, since I regularly am high in the mountains where the outside air temperature can easily dip towards 20°F, and sometimes as low as 0°F. Moreover, under those conditions I not only want to use the batteries (space heater!) but to run the engine for a short while to keep them charged if possible.
I learned that while discharge is OK in sub-freezing temperatures, lithium batteries can be damaged by charging if the internal battery temperature is sub-freezing. Discharge will warm the battery, but how to know if it can be safely charged? That is, one might want a space heater or to use a microwave for hot water when cold, but I’d be idling the engine when it’s that cold—and I do not want to damage the batteries by so doing.
The good news is that there is an elegant solution to sub-freezing temperatures with lithium batteries: the Lithionics battery can be ordered with the internal temperature intervention sensor. This *internal* sensor prevents the battery from being charged when its internal temperature is too cold to charge, which would damage it. Other brands such as Ultimate Power have similar technology.
Seagate 22TB IronWolf Pro 7200 rpm SATA III 3.5" Internal NAS HDD (CMR)
SAVE $100